Revolutionary Pickups: GMC Hummer EV, Ford F-150 Lightning, Rivian R1T
The electric pickup truck marketplace has seen a surge in popularity, demonstrating that electric powered vehicles can compete with petrol-heavy options for tackling tough tasks. While the industry continues to grow, let’s take an in-depth look at how American battery-powered pickups are made via YouTube’s Frame channel.
At the newly-rechristened Factory Zero, General Motors manufactures the highly-anticipated Hummer EV. Constructed upon GM’s Ultium platform architecture, the same framework that supports the Cadillac Lyriq and Chevy Silverado EV, this all-electric model promises to make a substantial impact.
Clay sculpting is utilized to construct the prototype model. After being finished, the vehicles are tested with six-axis robots that adds the primary layer of coating.

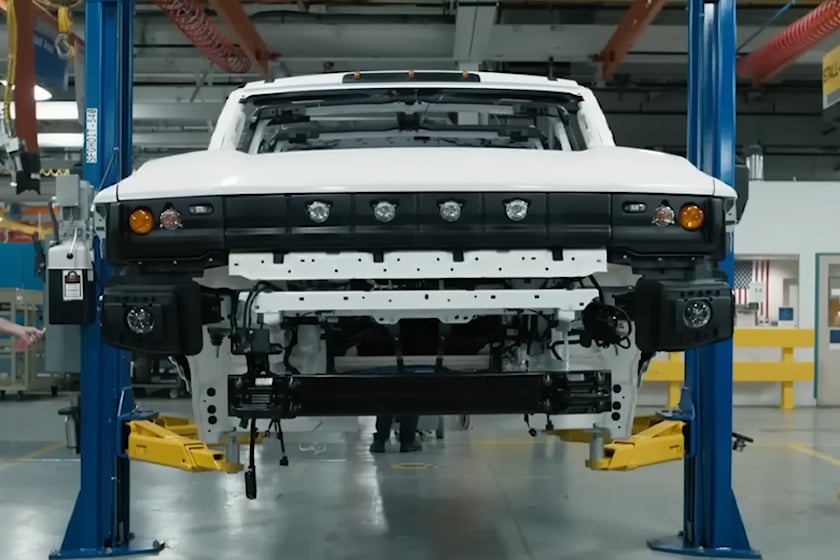
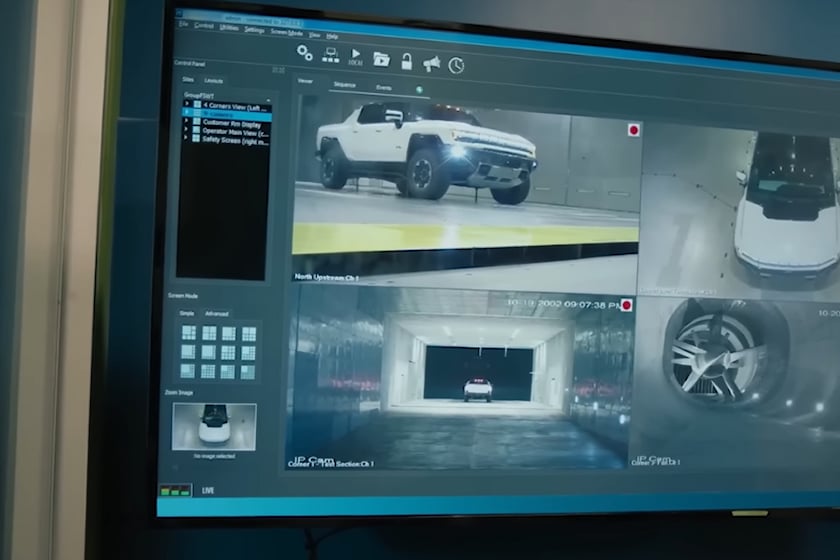

The priming layer is then subsequently overlaid with a clearcoat, furnishing a lustrous finish as well as safeguarding against UV radiation, scrapes and other external influences.
In regards to the battery pack, a procedure of electrolyte replenishment is executed in order to introduce a dissolved lithium-based salinization into the cells, allowing for a free exchange of ions between the battery’s poles.
On completion of the electrolyte fill procedure, the battery pack is installed beneath the car using an upper conveyor apparatus. The GMC Hummer EV holds the potential to produce 1,000 horsepower and guarantees up to 355 miles of operation on one charge.
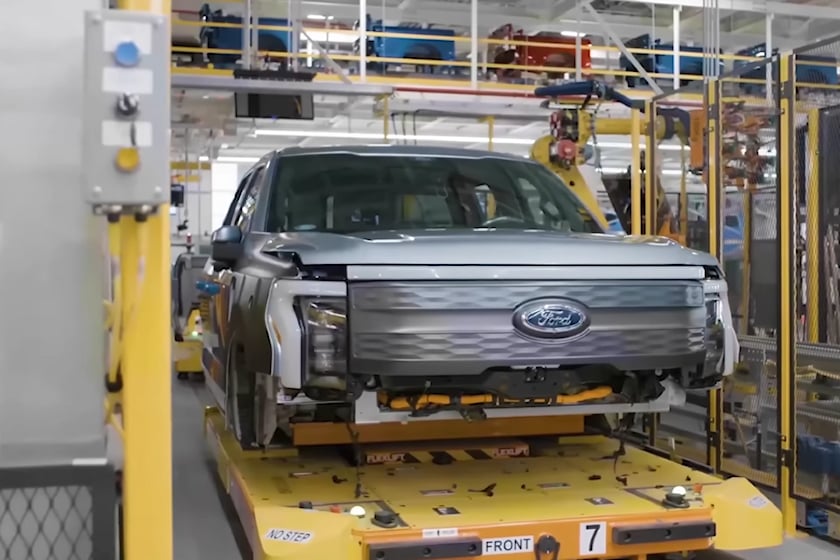
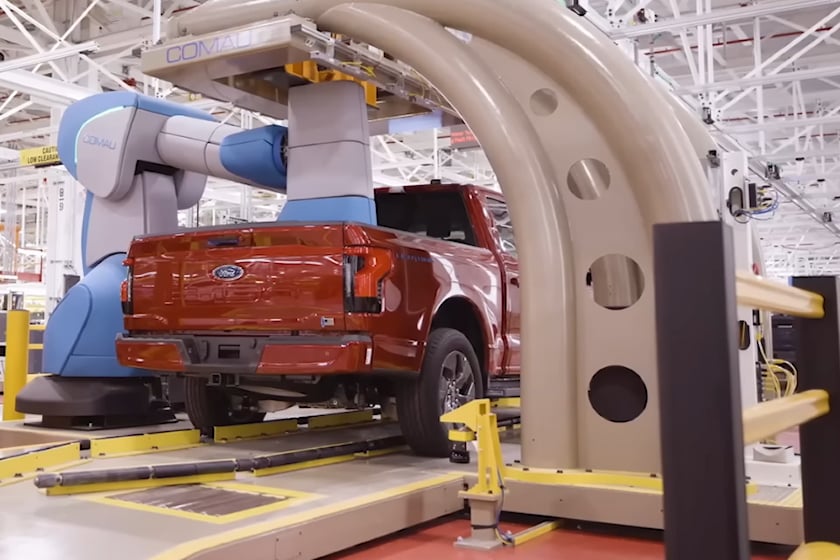

The following obstacle on the docket is Ford’s Rouge Electric Vehicle Center, which produces the F-150 Lightning electric pick-up truck. A lot of sections are added to the vehicle during production with minimal or no reliance on automation, inclusive of the front grille and cockpit console.
Ford Motor Company is looking to revamp their EV program with a massive $3.5 billion battery plant placed in Michigan’s Marshall. Together with China’s Contemporary Amperex Technology Limited (CATL), the Blue Oval company intends to bring down the cost of their electric vehicles such as the F-150 Lightning and Mustang Mach-E.
On their final stop, visitors explore one of Rivian’s main production plants in Normal, Illinois, where the R1T is manufactured. Apparently using a Komatsu Pressing Line machine, the metal sheets are fashioned into body panel components.

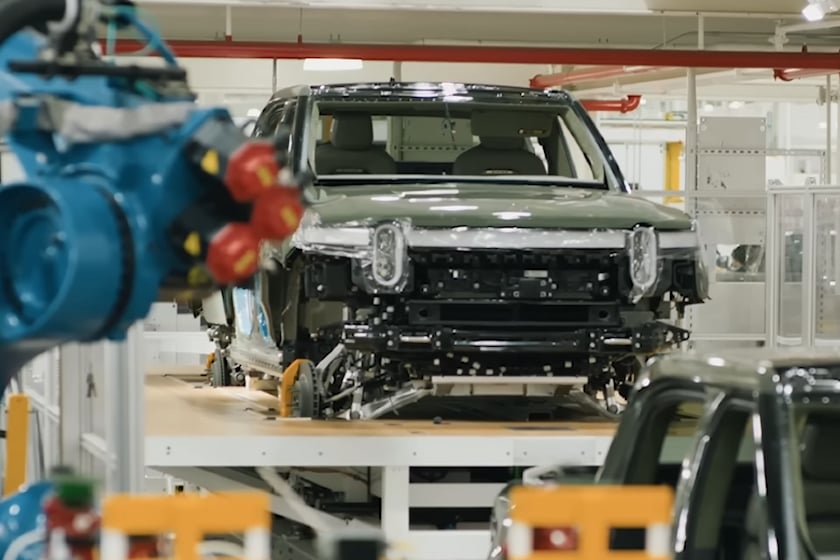
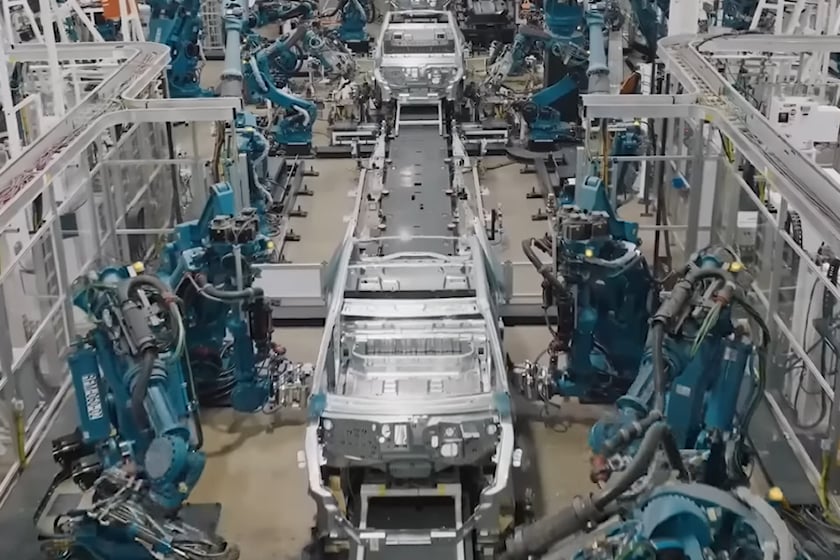
Robots of six axes, in automated fashion, are utilized by Rivian for joining the various metal parts together. During this spot welding activity, with the aid of copper electrodes to apply potency and warmness, an economical and faster process than regular welding is created as a weld.
Every wheel is furnished with Bosch’s 415-horsepower AC permanent magnet motor. Once the wheels have been set up, the truck experiences the Vehicle Alignment procedure, which uses laser sensors to quantify the camber and toe angles of the wheels.
Recent reports have indicated that GMC, Ford and Rivian will collaborate with Tesla to enable their electric vehicles (EVs) to use the Tesla Superchargers. From 2024, these three American auto giants will accept the North American Charging Standard (NACS) plug, thereby granting their EVs admittance to Tesla’s approximately 12,000 charging points in both the US and Canada.
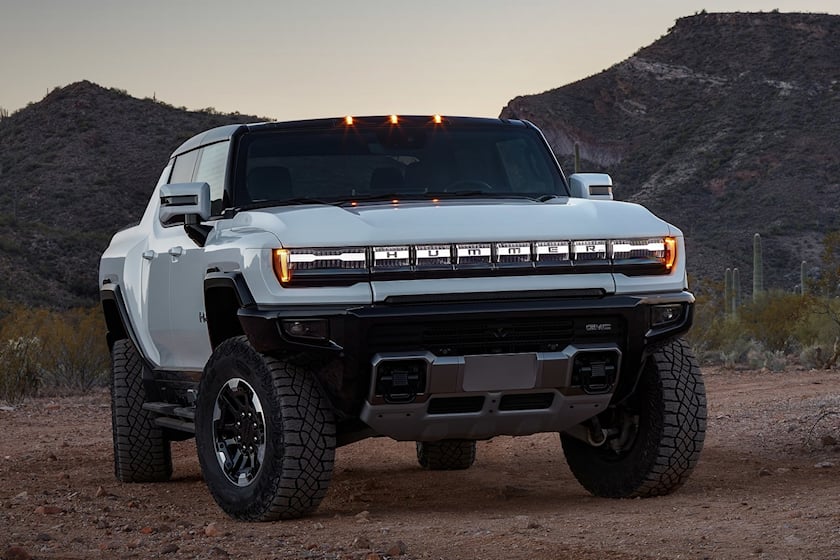
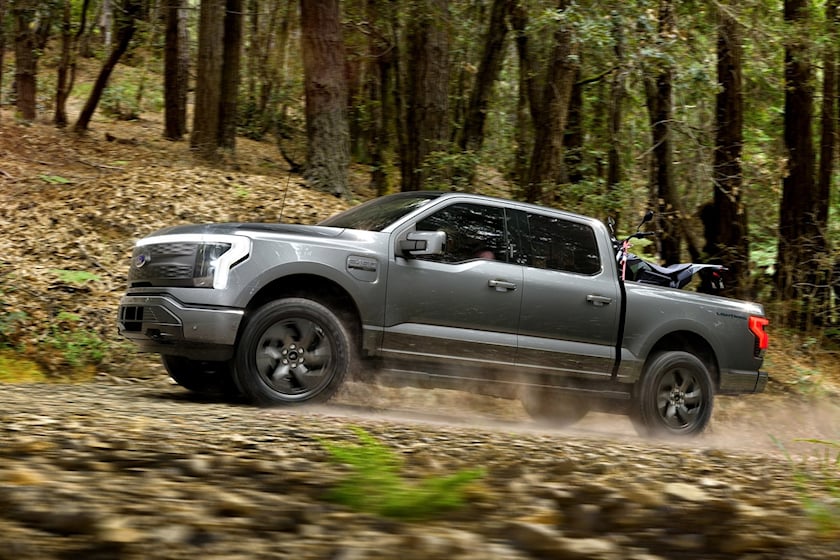
