Cooling Electric Motors for Performance and Longevity
In pursuit of assuring maximum EV utility, Rivian has developed a method to reign-in the heat levels in essential components of electric motors. Info spotted by CarBuzz at the United States Patent and Trademark Office (USPTO) hints at this fresh cooling technique from Rivian, suggesting that impending R1S and R1T models could be provided with more dependable performance and heightened durability.
Battery packs have relatively sophisticated temperature regulation mechanisms. For the reason that battery capability is reduced at freezing temperatures and batteries can come to ruin at soaring temperatures, equipment are in use to sustain battery core temps near 25° Celsius (77° Fahrenheit). That is nearby the ideal battery temperature in order to guarantee a harmonization between efficacy and longevity, typically obtainable by means of fluid-based closed-loop cooling systems.



Electric motors are often touted for their simplicity, as they don’t require any kind of pressurized lubrication. However, it is critical that their vulnerability to temperature variation be taken into account, as they will only perform optimally within a designated range.
Temperature control is a critical factor when integrating electric motors, as they necessitate that heat dissipation and battery output be kept apart. Indeed, the temperature thresholds of the two systems differ significantly. Implementing traditional temperature management approaches come with a number of challenges due to the complex and dense formation of motor windings. Fortunately, existing techniques are partially successful in dealing with this issue.
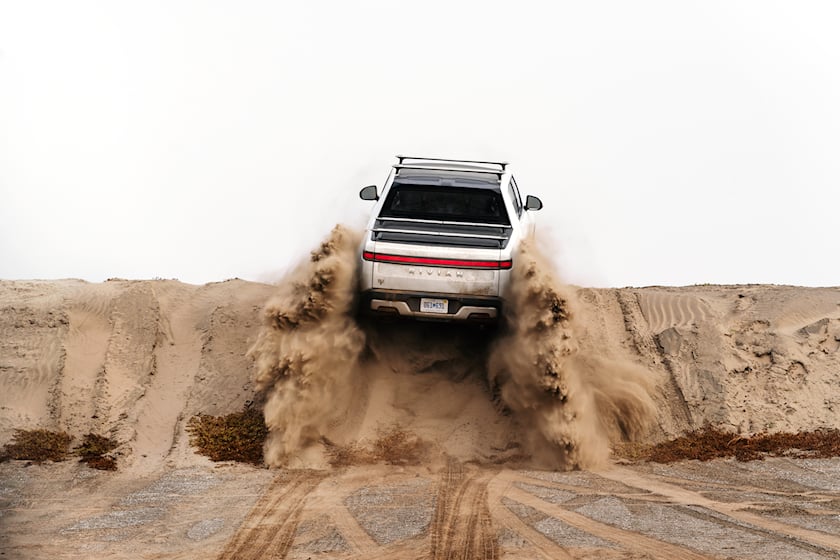
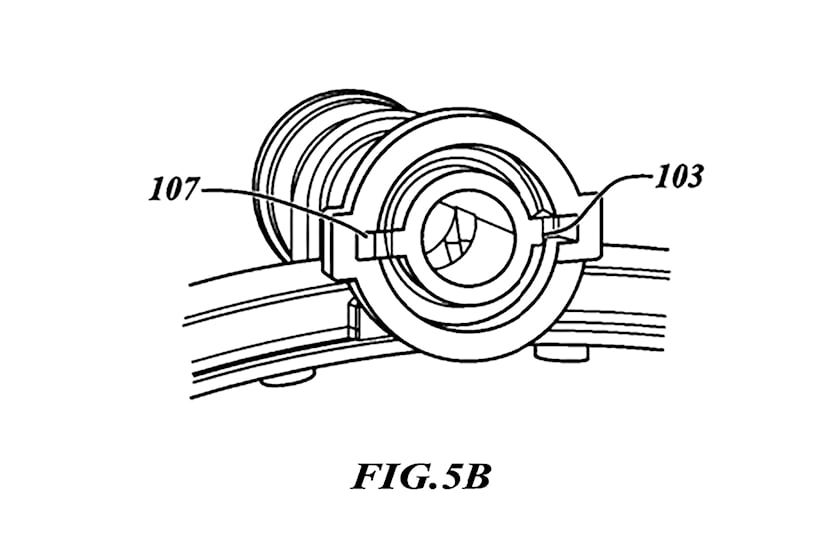
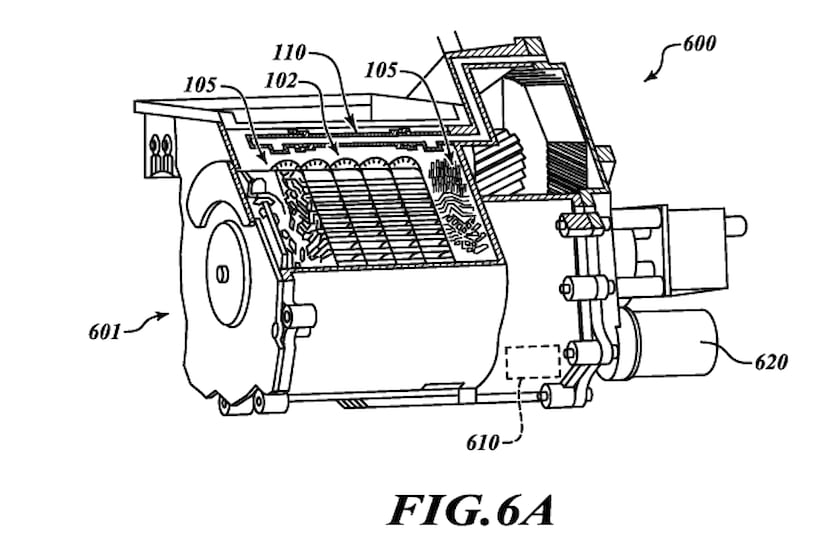
At present, concentrating on cool base plate cooling is the current standard conditioning for electric vehicles motor cooling. This means placing the motor component on an appropriately cooled heat sink, however air cooling is still an option although this becomes increasingly impracticable when the motors grow to be of higher power. As a further illustration, Tesla optimizes transmission and reduction gear oil for extracting heat from the stator, though this necessitates latter-mentioned designing compromises.
Traditional closed-circuit cooling of an electric motor is quite problematic to accomplish, largely because it is hard to regulate liquid flowing through the solidified windings. Moreover, in comparison to a battery assembly, the shifting components inside an electric motor might cause sealing difficulties and make construction more complicated.

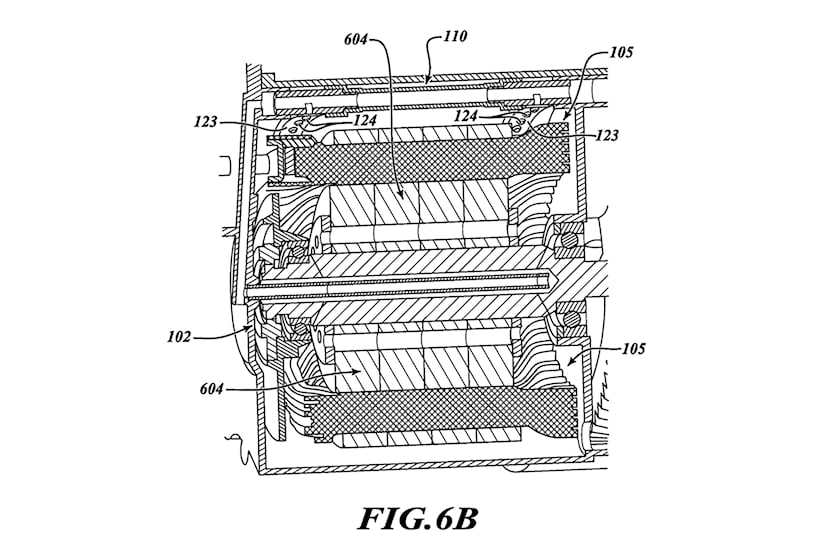

A fresh patent by Rivian proposes utilizing coolant dispensers on the external stator windings with a view to addressing this issue. The liquid could be an oil-drenched electric motor lubricant or a special insulator derived from purified synthetic oil. Supplying the stator windings with the coolant douses them with this fluid.
The oil sump serves to catch the coolant upon its passage through the coils, then circulating it via an electronically operated pump to a heat exchanger and returning to the stator. Through this precise control of motor temperature, it offers consistent performance and a decreased risk of shock damage to the windings. As a result, the life expectancy and operation of the motor will be extended despite any level of exertion on its part.
It is presumed that these improvements will be present in more advanced renditions of the company’s existing wares, or possibly they will just emerge a few years down the line. In order for EVs to prosper, they should become increasingly effective, and Rivian is committing all their efforts to reaching this objective.

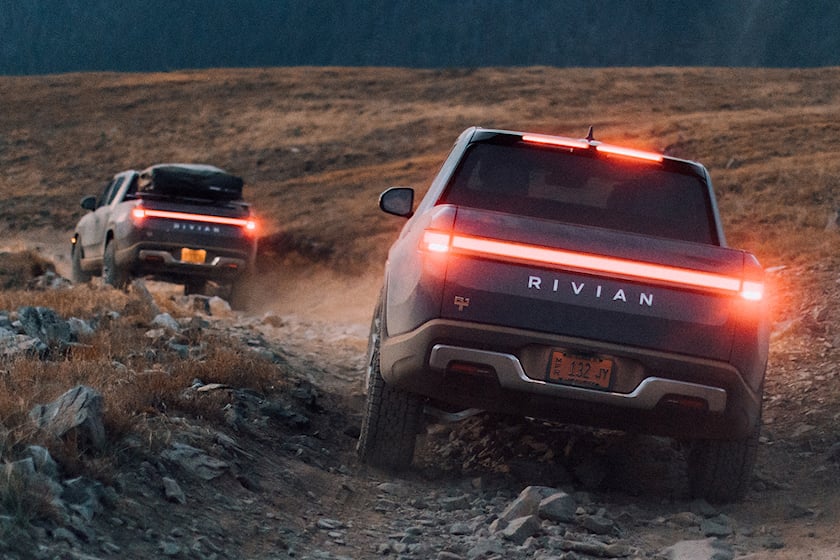
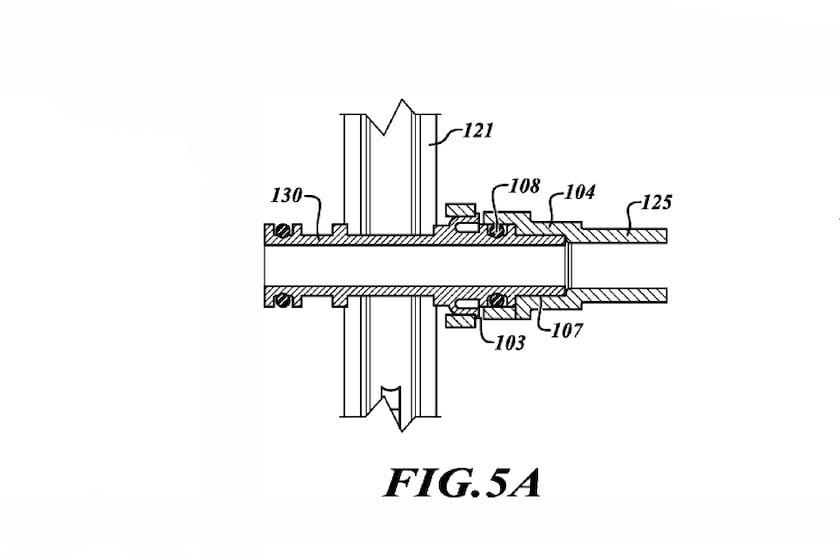
I loved this article blog_title ! I check your blog fairly often and you’re always coming out with some great stuff. I shared this on my FB, Instagram and my followers loved it ! Maintain the good work 🙂 !