Inexpensive solution to repair scrapes on parking lot bumpers without repainting.
BMW has secured a patent for an innovative technology which would revolutionize the production of exterior trim panels. Instead of traditional painted plastic, these panels would be crafted from unpainted plastic and treated with laser radiation to achieve different textured patterns. This method not only enhances the durability of the trim pieces but also promotes eco-friendliness. Additionally, it significantly reduces the visibility of any potential damage caused by stones or scratches, making expensive paint repairs obsolete. The use of this technique is particularly advantageous for premium vehicles such as the BMW 7 Series where paint options can come at a hefty price. Therefore, it is logical for BMW to consider implementing this technology.
A recent patent, discovered by CarBuzz from the German Patent and Trademark Office (DPMA), details the usage of plastic body panels in vehicles and how they are usually coated with paint. However, this method is not only costly but also contributes to a larger impact on the environment. While some car companies have experimented with unpainted plastics for certain surfaces, their results have been inconsistent. BMW asserts that those who purchase luxury products desire a sophisticated appearance, making traditional unpainted plastics inadequate.
BMW has presented a solution involving plastic mixtures containing diverse pigments that respond to radiation by altering their hue, ultimately unveiling distinct designs.
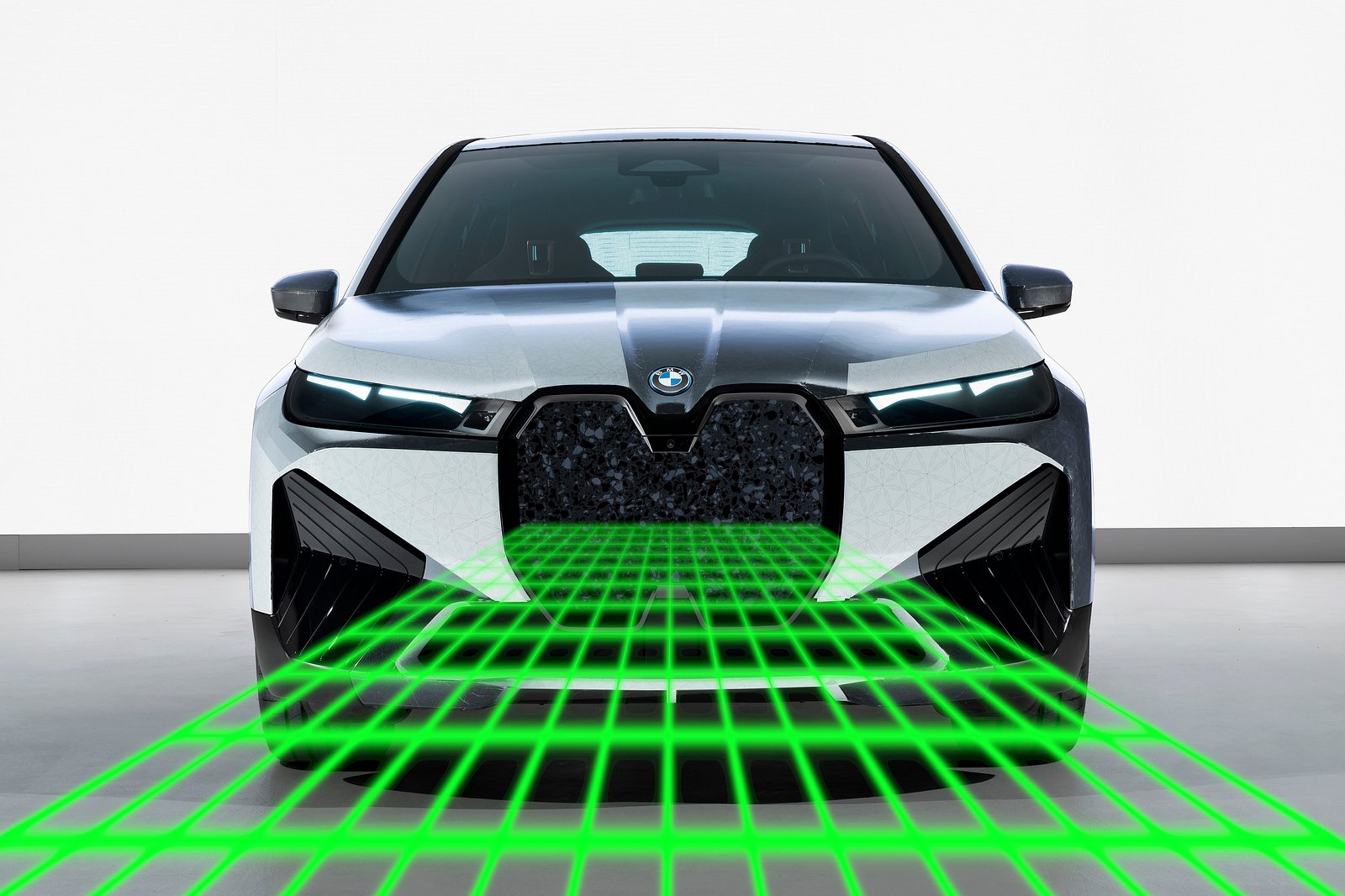
The emission of radiation would result from the use of lasers, similar to the way in which laser etching creates diverse patterns and appearances on various substances.
The patent details the use of a design resembling stone or terrazzo being carved into the plastic material. Terrazzo, a type of stone made from cement and minerals like marble and granite, serves as an inspiration for this pattern. However, there is room for exploration in creating asymmetrical visual textures. These could possibly replicate the look of forged carbon fiber or quartz.
BMW has a conceptualization for implementing this procedure in the production of bumper trim, inserts, diffusers, and/or sill trims. Various plastic components such as wheel arch cladding, grille surrounds, and many other small parts could also greatly profit from this innovation.

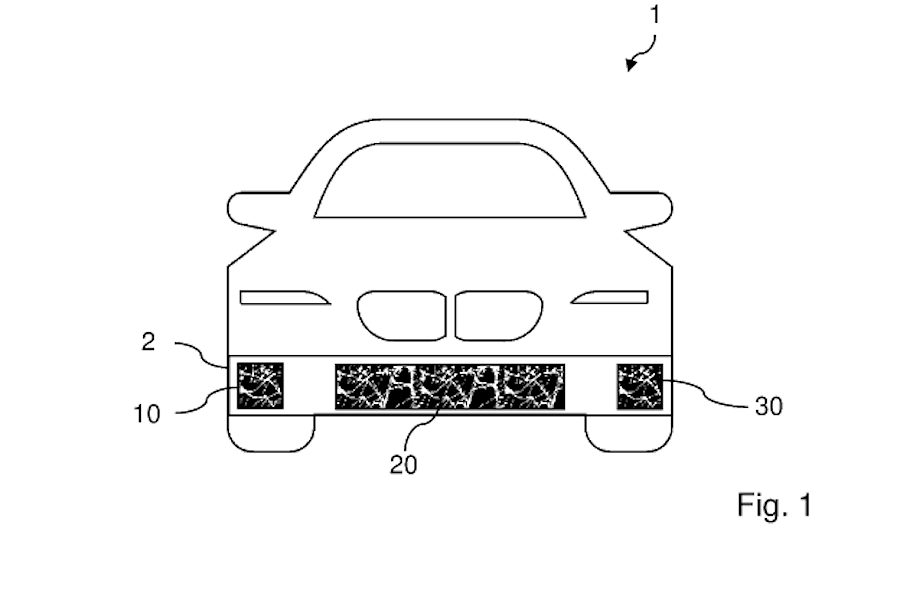
The panels would possess a one-of-a-kind appearance while also boasting impressive durability. This is due to the fact that the entire component, whether it is part of the body or serves as a trim panel, will be constructed from plastic polymers that have been infused with dye. As a result, minor damages such as shallow scratches and stone chips will not significantly affect the overall appearance and texture of the material, unlike chipped paint or deep scratches. Thus, there will be a decreased necessity for replacing, fixing, or detailing these panels.
The irradiation process triggers a chemical response that permeates beyond the top layer, rendering even deep scratches inconsequential when it comes to leaving visible marks.
Not everyone excels at parking, even with the assistance of modern park assist technology. It’s a common occurrence to scrape plastic bumper trim in parking lots. However, thanks to this innovative method, such occurrences will no longer be as noticeable as scratches on painted surfaces.
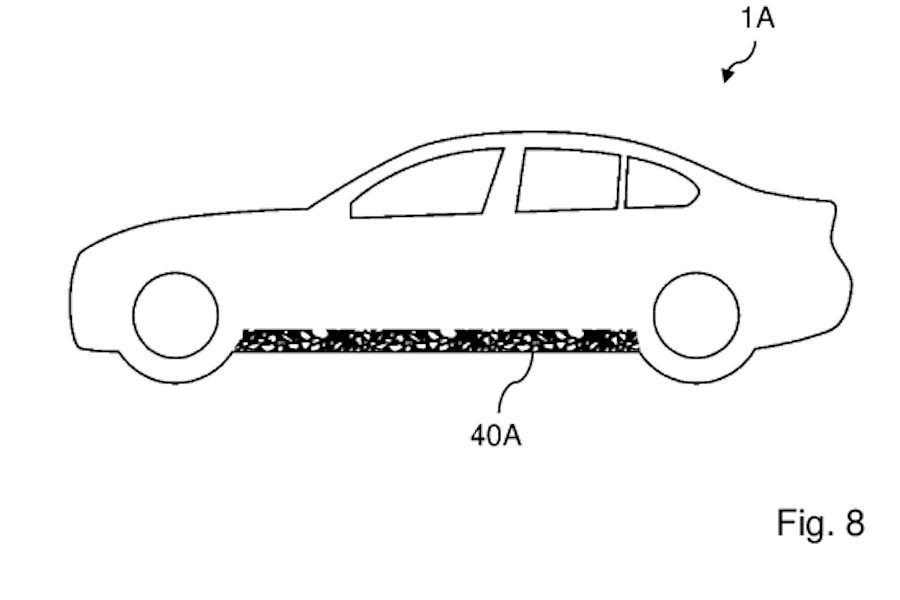
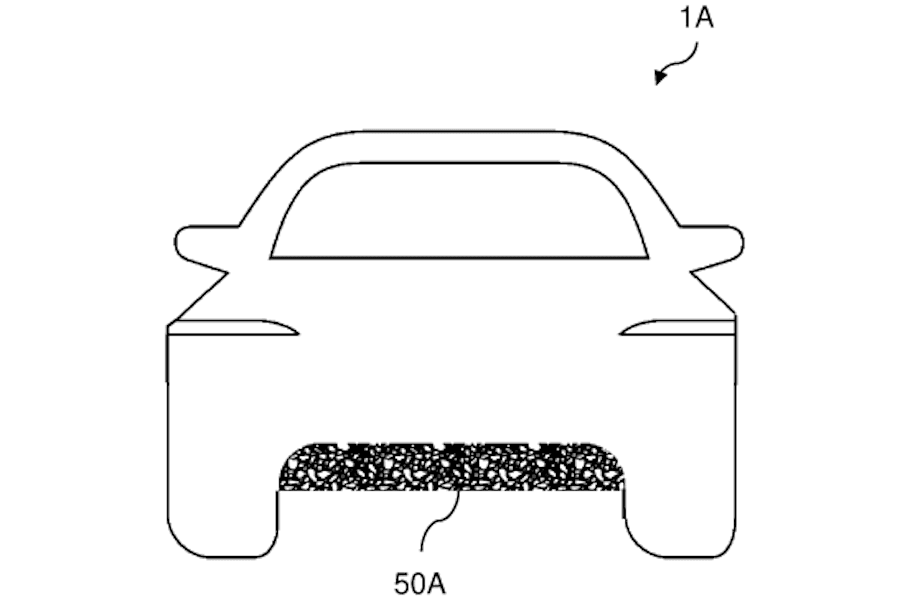
As per BMW’s assertion, this leads to enhanced sustainability and diminished production of parts, as the plastic panels do not require painting, making them more recyclable for future vehicle production.
The concept of sustainability is further reinforced by the use of recycled materials or biodegradable plastics derived from vegetable oils and fats in the production of plastic panels. This shift away from petroleum-based plastics contributes to a more environmentally-friendly approach.
According to scientific principles, irradiation usually leads to carbonization or the formation of tiny carbon dioxide bubbles in materials (resulting in a darkening or whitening effect, respectively). However, through the use of different dye pigments, a wide range of colors including red, yellow, blue, and other shades can be produced.
In addition to this, BMW is using E-Ink technology for color-changing body panels and incorporating crystalline headlight structures, signifying a revolutionary shift in the design and construction of future cars.
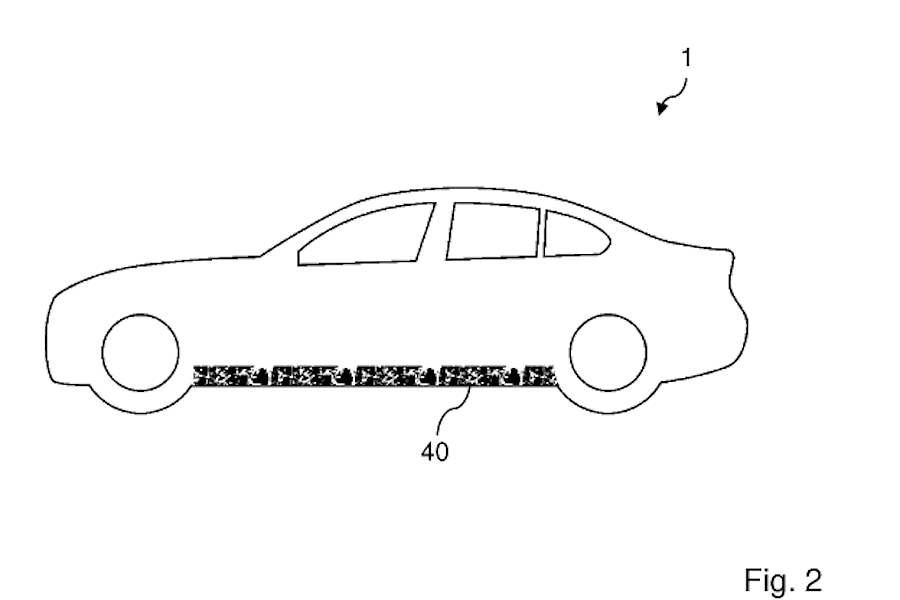